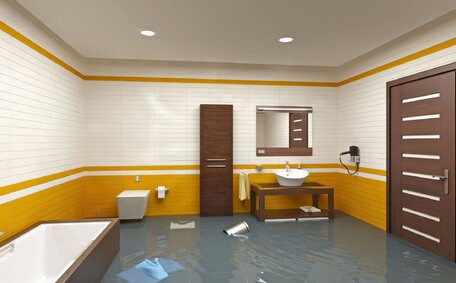
Signs Your Hot Water System Is Failing
Common signs your hot water system is failing include strange noises, rust, leaks, inconsistent temperature and pressure. Call our licensed plumbers if you notice these issues for repairs.
Read MoreA properly maintained hot water system is essential for the comfort of your home and the functionality of any business. Routine plumbing maintenance is the safety net for your hot water heater, assuring efficient and reliable operation into the future.
This article provides you with a practical water heater maintenance checklist that home and business owners alike can execute with ease. We’ll cover inspections, testing important parts like temperature and pressure relief valves, checking anode rods, draining and flushing tanks, and more.
Following the recommended preventive maintenance tips here will optimise performance and prevent issues like leaks, corrosion, sediment buildup, and early system failures. That means you’ll enjoy lower energy bills, fewer costly repairs, and hot water whenever you need it.
Maintaining consistent temperature and pressure in your hot water system is crucial for daily activities. Taking good care of your system with regular maintenance pays dividends through enhanced safety, efficiency, and longevity your investment.
It’s essential to carry out maintenance on hot water systems biannually or annually to ensure optimal functionality.
A licensed technician will rigorously assess your system, including valve tests, pipe connection security, and anode rod inspections during maintenance checks. Preventative maintenance helps extend the lifespan of water heaters by 5-10 years.
Key benefits gained from this inspection checklist include:
Committing to get your maintenance checks once every six to twelve months as part of your regular home care ensures the reliability of your hot water system for the foreseeable future.
Inspecting your hot water system every 6-12 months is a key part of preventative maintenance. A comprehensive inspection by a licenced plumber should include the following:
Start by shutting off the water supply to the hot water system. This allows you to safely inspect components without any water flow.
Carefully examine the pressure relief valve, temperature relief valve, vacuum relief valve, and gate/stop valves. Make sure they are in excellent working condition with no signs of wear, corrosion, or leakage.
A technician should manually operate the temperature pressure relief valve to guarantee correct operations. Check that the drain lines from the relief valves are free-flowing and terminate appropriately.
Check anode rods, which act as sacrificial elements, protecting the tank from corrosion. Replace it if substantially worn down.
Examine the water heater tank and connected pipes for any signs of corrosion, leaks, or damage. Fix any minor issues immediately.
Once the water supply is reestablished, check the flow rate of hot water from nearby taps. Verify adequate and stable water pressure.
Following this thorough heater maintenance checklist helps ensure safety and peak performance. Identify and address minor problems before they become major repairs down the road.
Visually inspecting your hot water unit and connected pipes during maintenance checks is crucial for identifying potential issues early. Look for signs of leaks, corrosion, damage, or unusual water puddles surrounding the unit.
Check where pipes connect to the hot water heater for drips, rust accumulation, or water stains. Give careful attention to the control valve, relief lines, fittings, and pipe joints as well. Even minor leaks can lead to substantial water damage over time if left unaddressed.
Should you spot leaks, corrosion, or other damage, reaching out to a licensed plumber without delay is critical to halt the progression of such issues. Catching minor issues now can help save you from more expensive repairs down the road.
Visually surveying your hot water system and your pipes takes just minutes but provides invaluable awareness of developing issues before they cause hot water failures, flooding, or other serious problems.
Testing the valves on your hot water system during maintenance checks is vital for safety and efficiency.
Test the pressure relief valve on your gas water system by lifting or twisting the lever; a proper discharge of water signifies it’s functioning to avert overpressure. Check that the discharge pipe allows water to drain away safely.
Turn up the temperature setting on your water heater to activate the temp relief valve. Hot water should discharge from the valve once the predetermined safe temperature is exceeded. Lower the temperature setting when flow is verified.
Confirm the backflow valve is operational by ensuring there’s no water movement when checking with the cold water on and hot water turned off.
Testing these crucial valves ensures your system can safely release excess pressure or temperature, preventing explosion or scalding hazards. Malfunctioning valves should be replaced immediately by a qualified technician.
Over time, sediment can accumulate at the bottom tank of your hot water system, leading to inefficiency.
Your efforts in draining and flushing your water heater’s tank play a significant role in sediment removal and lifespan extension. This maintenance task should be performed annually.
Use these steps for efficient tank drainage:
Draining your water heater regularly removes sediment, enhancing efficiency and reducing the risk of early system failure—a simple yet vital task.
Having your anode rod examined is one of the most vital steps to prevent any undue hot water system maintenance woes. This sacrificial metal rod protects the heater tank from corrosion but requires replacement every 3-5 years as it deteriorates.
It’s essential to closely examine your anode rod during these inspections. Look for significant downward tapering, a reduction in diameter of 50% or more, heavy pitting or chunks of the rod missing. Any of these signs means it’s time for a replacement.
A new anode rod can significantly restore your tank’s defence against corrosion, a cost-effective preventive measure that can lengthen the system’s lifespan.
Proactive anode rod replacement is much cheaper than having to buy a whole new hot water system.
Don’t neglect this invaluable protective component. Make examining the anode rod a key part of your regular water heater maintenance routine.
Replacing the anode rod every 3-5 years is crucial to extend your hot water system’s lifespan and prevent tank corrosion. For optimal results, examine and, if necessary, replace the anode rod once every six months to a year, especially when there’s significant wear.
Please watch for the following signs indicating a need to replace your anode rod:
Hard water may necessitate more frequent anode rod replacements. Replace deteriorated rods promptly to maintain effective corrosion prevention.
Replacing the anode rod as needed provides maximum corrosion protection and can extend the life of your hot water system by up to 10 years. It’s inexpensive insurance to safeguard your investment.
Proper refilling of the hot water system’s tank after drainage is critical to prevent damage. Adhere to the following steps:
Taking the time to correctly refill your hot water tank prevents issues like pressure spikes, water hammer, and leaks leading to corrosion or cracks over time. It ensures your heater returns to service safely and efficiently after maintenance.
A professional plumber’s inspection of your hot water system offers advantages that surpass even the most thorough DIY maintenance.
With extensive training and years of hands-on experience, plumbers can spot subtle problems in your plumbing or recommend upgrades the average homeowner might overlook. They have specialised tools, testing equipment, and the expertise to thoroughly assess all components.
In commercial settings with complex water heating systems, a comprehensive plumbing maintenance strategy is recommended. Commercial and industrial sites with large volumes or strict compliance codes also require qualified inspections.
Even straightforward residential heaters will benefit from professional oversight every 2-3 years. Consider professional inspections as fine-tuning for optimal safety and efficiency of your water heating system.
Regular maintenance services from a trusted plumber safeguard your investment and prolong the system’s life, resulting in long-term savings. Periodic professional checkups complement regular owner maintenance.
Signing up for reminders and maintenance plans from a professional plumbing company like Marrickville Plumbing can make caring for your hot water system worry-free.
We provide automatic reminders for inspections, ideally every six months, to keep your system in top condition. Our licensed technicians execute an exhaustive maintenance check in accordance with industry best practices.
You can also enrol in one of our preventative maintenance plans. We’ll inspect, test, and tune-up your hot water system on a regular schedule to optimise safety and efficiency. This helps prevent unexpected breakdowns and extends the operating life of your heater.
Contact Marrickville Plumbing today at jobs@marrickvilleplumbingservices.com.au or call 1300 349 338 to learn about our reminder services and maintenance plans. Our experts are ready to assist with all your hot water system needs.
Common signs your hot water system is failing include strange noises, rust, leaks, inconsistent temperature and pressure. Call our licensed plumbers if you notice these issues for repairs.
Read MorePipe relining is an eco-friendly alternative to pipe replacement that uses materials like epoxy resin to repair pipes without digging. It produces less waste and emissions than traditional methods. Learn about the environmental benefits of trenchless pipe relining.
Read MoreReplacing an outdated electric, gas or solar hot water system with a more efficient heat pump or solar model can significantly reduce your energy bills and carbon footprint. Take advantage of available rebates. Contact us to retrofit your old system today.
Read MoreMarrickville, 2204 NSW
We will call back as soon as possible.